船舶生产车间管理系统
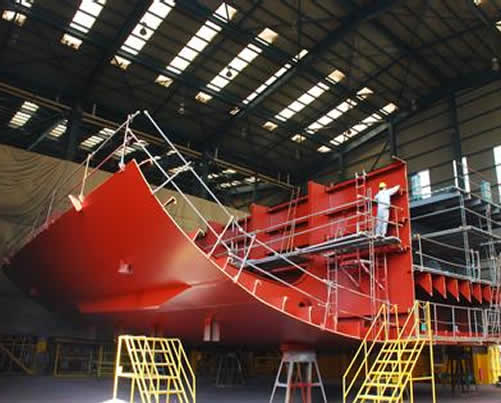
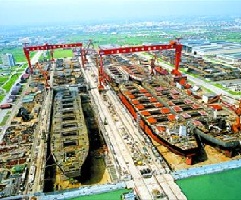
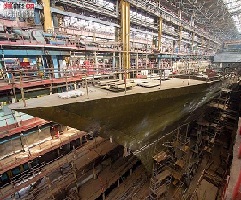
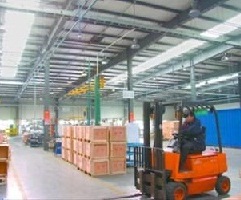
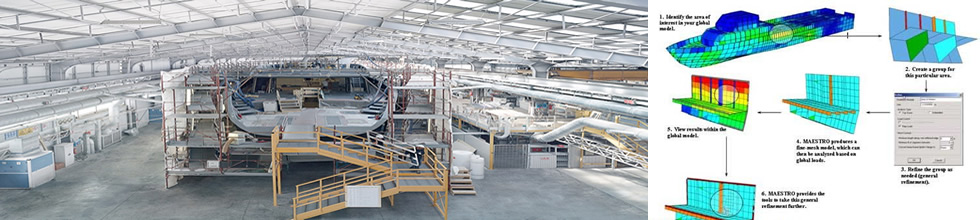
目标:运用网络化和数字化技术,为用户实现产品全生命周期管理
船舶行业属于离散型制造行业,船舶产品制造有两大特点:一是多品种的小批量生产,二是综合性的总装配生产。船舶行业必须全面建立现代造船模式,切实转变经济增长方式。
现代造船模式是以中间产品组织生产为基本特征的总装造船模式,主要由统筹优化的造船理念、面向生产的设计技术、均衡连续的作业流程、严密精细的工程管理和高效合理的生产组织等基本要素构成。现代造船管理模式的核心是以"中间产品"为导向,按区域、阶段、类型进行设计,有效、均衡、连续地组织造船生产。在现代造船模式下的工程管理特点主要有五点:以"中间产品"为导向来分解船舶工程;按"中间产品"的类型和阶段来组织生产;以混合工种、复合工种和一专多能来组建综合性施工班组;按区域、分道进行生产管理。
造船工程在开工之前应对整个工程进行分析、解剖,分解成许多子工程以利整个工程的顺利组织和实施。传统的造船模式是以船舶的功能、系统来分解工程。现代造船模式的工程分解是将整个船舶产品分解成一个个"中间产品",这些"中间产品"实际上是船舶产品的一个个组成部分。分解成的一个个部分是按层次,即按船舶制造的程序来划分的。每一个制造程序称之为制造级。这些中间产品经过装配逐渐变大、变复杂,最终形成一艘船,即最终产品。现代造船模式的以"中间产品"为导向,即把对整个船舶产品的生产管理,变成围绕生产"中间产品"的管理,就是"以中间产品为导向"。 车间管理必须依据上述特点进行组织和管理。
船舶的建造是一个复杂的系统工程。按船舶制造加工手段分,船舶中间产品可以分成三大类:
(1)制造工程类
船舶制造工程类的中间产品是指将原材料通过加工,使其形成可以安装、装配的零件、部件和构件。这类中间产品在制造过程中改变了原材料的形状,在工艺上通常是经过热加工或冷加工的办法使其变形。如:板材/型材,先通过切割形成各种零件,再通过冷热弯曲等变形,形成曲面板件和曲型材;管子,先通过冷热弯制,再通过焊接形成管件等。在船舶制造过程中,该类中间产品数量巨大,达到几十万种,但制造工艺类型相对较少,通常采用典型工艺对相同制造要求的零部件加工工艺进行定义。在典型工艺中对零部件的加工工序、工作内容、加工中心和检验要求等内容进行参数化描述,车间管理在获取任务包的物量后能够根据典型工艺参数,进行车间作业计划和加工中心资源管理。
(2)安装工程类
船舶安装工程类中间产品是指用各种联结方式,将部件、零件等进行组装和装配,它基本不改变零件、部件和组件的状态,而是把它们进行固定和组合。如:船上机电设备的安装、管子的安装、分段的装配、总段的合拢等。安装工程类中间产品在工艺方面主要涉及到各类安装和装配工艺,如铆接、栓接、焊接等的。船舶通过安装工程后,一个确定状态的船就形成了。该类中间产品工艺主要是焊接工艺、安装工艺。
(3)试验工程类
试验工程可分为系泊试验和航行试验。系泊试验解决的是系统的畅通性、正确性,各系统设备的完整性、功能的协调性等。航行试验是对建造后的船舶的实际情况进行考核和检查,获取试航数据等。试验工程是以试验项目为中心的项目管理。
以中间为导向的车间管理不同于传统制造车间管理。它是以总装化思想为先导,结合专业性和综合性形成相对封闭的责任单元。在生产计划驱动下,按作业指令完成中间产品制造,是适应以管理的质量、进度及成本等三要素可控,达到利润最优化目标。
由于中间产品对象的差异,必须根据中间件制造特征建立不同的制造车间,建立与之适应的车间管理模式。典型制造车间包括:集配车间、船体零件制造车间、管子零件制造车间、分段制造车间、舾装车间、涂装车间、船台车间、码头车间等,分别承担了物流配送、中间件生产、总装生产、船舶试验各阶段的生产任务。 不同车间的生产对象、组织方式各有不同。通常分为集配车间、零件制造车间、装配车间、试验车间。
(1)集配车间是物流管理的关键环节,主要生产任务进行托盘集配,按照出托计划进行托盘配送。集配车间管理主要包括:出托计划管理、物资到货情况查询、托盘集配、出托任务管理及反馈。
(2)零件制造车间主要按照安装托盘计划进行零件制造。安装托盘计划由船舶制造主生产计划确定。车间生产根据典型工艺,按照成组性原则组织。在零件制造车间,存在大量的数控设备,如,数控切割机、数控弯管机以及数控机床等。对数控设备的有效管理是车间管理的一个重要方面。零件制造车间管理主要包括:车间任务管理、车间看板、派工单管理、作业单元管理、数控程序管理、制造质量跟踪统计等。
(3)装配车间主要按照工程结构进行托盘装配。装配过程中,船台吊装是船舶建造中的主计划,驱动着制造计划和配套计划。
(4)试验车间主要按照船舶各系统进行调试和试验,车间管理按照项目管理方式组织。
解决方案特点
功能需求
船舶生产车间管理系统核心功能包括:
(1)车间作业计划管理
车间作业计划是在造船工程计划基础上,编制不同制造级中间产品的作业计划,并对计划进行考核。由于车间作业对象的生产工艺和流程不同,生产组织上存在很大差异,车间作业计划方式不同。
(2)车间任务管理
车间任务管理主要对作业任务进行分派,指定作业班组或作业单元。车间任务管理中一项重要工作是保障车间关键工作中心任务均衡。
(3)集配管理
集配管理是造船物流一个重要的控制环节,根据造船工程计划将各类物资以托盘为单位,送到安装区域。集配管理主要包括了出托计划编制、物资配套和送托等工作。在集配管理过程中需要了解和掌握造船工程进度、物资到货情况和运输工具负荷情况。
(4)车间工作中心管理
车间工作中心管理是车间的一项基础管理工作。车间工作中心的定义必须结合车间生产组织模式。工作中心可以是一条流水线、也可以是一台加工设备或是一个班组。工作中心设定后,必须对工作中心能力进行测算,提供给车间工艺管理和计划管理人员进行工艺设计和计划平衡。
(5)车间人员管理
车间人员管理是车间的一项基础管理工作。该项管理是人力资源管理的一个环节,用于及时、动态了解车间人员状况,如出勤、工作负荷、工作质量等。
(6)制造质量监控
制造质量监控是根据车间质量管理的关键手段。制造质量监控从作业检验情况中分析统计,得出车间作业质量状况,建立各工序的"跟道卡",监控作业设备、人员操作、材料质量等影响作业质量因素,提高制造作业质量。
(7)车间作业任务反馈
车间作业任务反馈主要针对作业任务单(派工单)的实际完成情况反馈,反馈的重点在物料批次的跟踪。通过该项管理,不仅使车间作业计划得到及时反馈,更重要的是实现了物资批次的跟踪管理。
(8)数控程序管理
数控程序管理是车间管理到设备控制间的一个重要的管理环节。主要提供数控程序编制、工艺模拟、数控程序版本管理,与数控设备通讯管理等。
技术创新
(1)综合利用船舶三维设计的虚拟动态监控技术、产品装配工艺过程的仿真演算、仿真时钟推进下船舶生产流水节拍模拟控、零部件制造级数字化车间仿真分、数字化船舶总装物流仿真技术和虚拟现实系统配置技术;
(2)减少因装配干涉等问题而导致的重新设计和工程更改,提高制造信息集成度,减少资源浪费;
(3)强化各部门的协调能力,实现并行工程,减少技术决策风险,降低技术协调成本,使制造单位能适应激烈的市场竞争和不同的用户需求;
(4)产品装配周期平均可缩短30%,通过数字化预装配和装配过程仿真优化技术替代零部件装配试验,可降低开发成本25%左右;
(5)有效减少装配缺陷和产品故障率,减少制造过程反复,降低人为差错80%以上。